Determining The Correct LED Driver Voltage Range for an LED Application
Viewers : 185
By Hank Lan/MWEU Technical Dept.
To select a LED driver with a proper voltage operating range (Constant Current region) may look fairly easy, but this article will explain that it is not that straight forward. Firstly, one has to realize that LED forward voltages are not identical from die to die. Secondly, the LED voltage varies when the junction temperature goes up or down. Since a correct working of the driver is crucial to the functionality and reliability of the lamp, it is worthwhile to look more into details of these factors which affect the LED voltage. This article explains the typical concerns of LED forward voltages and how to properly determine the needed margin for the LED driver voltage. It also suggests looking for a new function found in some new LED drivers that can work with a temporary increased output voltage to circumvent the issue of LED high voltage at extremely low temperature.The design of a LED lamp is a multidimensional engineering work which involves optical, thermal and electrical design concerns. To achieve the target of optical requirements, the type and the quantity of LED and its driving current are decided first. Depending on certain safety considerations and/or a modularized design approach, certain numbers of LED’s are put in the same string and others in parallel. When these factors are defined, the first estimation of LED working voltage can be made by multiplying the number of LEDs in one string to the typical forward voltage (Vforward) of this LED.
Vforward_total = Vforward x Num/String
The above calculation gives a rough idea about the operating voltage range and together with the determined driving current one will know the power requirement. However, this number is not an absolute value and not suitable to ensure a proper electrical design. To make the design concern on the driver’s voltage, the LED voltage should be considered by 1) V-I characteristic, 2) Production variation, and 3) Temperature coefficient.
In the paragraph below these 3 aspects are explained separately, and at the end of the article, an example of voltage estimation and LED driver choosing steps are provided.
LED V/I characteristics
For an ideal LED, the forward voltage does not change when current increases (Fig 1.). In reality, the forward voltage DOES change with current, and it is important to check the LED voltage based on the actual designed current instead of referring to the specification standard test condition.
In the example below, specification shows the typical voltage of the LED is 3.2V. If LED is not used at 350mA but 1A, then instead of 3.2V/LED, the actual typical LED voltage is 3.8V/LED. This 0.6V difference could lead to a very different result when a high number of LEDs are put in series. Furthermore, the situation can get even worse if the LED driver has a high ripple current which would result in a peak current higher than 1A and thus the peak voltage would exceed 3.8V.
LED production tolerance:
LED forward voltages on each die have variations due to process drift. A mature production should provide a tighter tolerance resulting in a normal distribution (e.g. Fig. 3). Typical voltage tolerance due to production variation is less than 10% which can be indirectly derived from the maximum-to-typical ratio on the typical forward voltage on LED datasheet (Referring Table 1 column 4 and 5). The production data like actual forward voltage distribution, on the other hand, might have to be checked with LED manufacturer directly.
Although the absolute maximum/minimum is +/- 10%, statistically, the more LED’s connected in series, the more likely the combined forward voltage will settle around the typical voltage value. It is recommended to create some voltage head room, a margin of 10% to the typical voltage is considered safe. A higher margin can be considered as well, which would put the driver in a better working condition and extends the drivers lifetime.
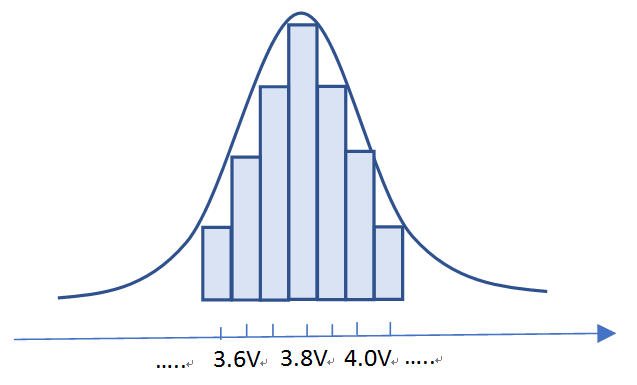
Fig 3 LED forward voltage distribution from production
In the paragraph below these 3 aspects are explained separately, and at the end of the article, an example of voltage estimation and LED driver choosing steps are provided.
LED V/I characteristics
For an ideal LED, the forward voltage does not change when current increases (Fig 1.). In reality, the forward voltage DOES change with current, and it is important to check the LED voltage based on the actual designed current instead of referring to the specification standard test condition.
In the example below, specification shows the typical voltage of the LED is 3.2V. If LED is not used at 350mA but 1A, then instead of 3.2V/LED, the actual typical LED voltage is 3.8V/LED. This 0.6V difference could lead to a very different result when a high number of LEDs are put in series. Furthermore, the situation can get even worse if the LED driver has a high ripple current which would result in a peak current higher than 1A and thus the peak voltage would exceed 3.8V.
Characteristics | Unit | Minimum | Typical | Maximum |
Forward voltage (@350mA, 85°C) | V | 3.2 | 3.48 |
![]() |
![]() |
Fig 1. | Fig 2. |
LED production tolerance:
LED forward voltages on each die have variations due to process drift. A mature production should provide a tighter tolerance resulting in a normal distribution (e.g. Fig. 3). Typical voltage tolerance due to production variation is less than 10% which can be indirectly derived from the maximum-to-typical ratio on the typical forward voltage on LED datasheet (Referring Table 1 column 4 and 5). The production data like actual forward voltage distribution, on the other hand, might have to be checked with LED manufacturer directly.
Although the absolute maximum/minimum is +/- 10%, statistically, the more LED’s connected in series, the more likely the combined forward voltage will settle around the typical voltage value. It is recommended to create some voltage head room, a margin of 10% to the typical voltage is considered safe. A higher margin can be considered as well, which would put the driver in a better working condition and extends the drivers lifetime.
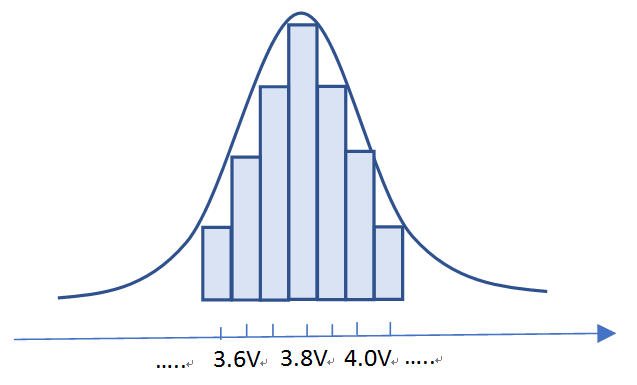
Fig 3 LED forward voltage distribution from production
LED Vf. Vs. Temp
The LED forward voltage has a negative temperature coefficient, this means the higher the temperature the lower the forward voltage. As a LED is a self-heating element, with a proper thermal design of the lamp, the continuous working temperature and LED operating voltage are normally quite stable. The worst case comes when the lamp starts up at a low temperature. To estimate the extra voltage requirement at low temperature, LED spec provides a typical V-T curve according to the standard test condition (e.g. 350mA). Many manufacturers also provide a software tool to check voltage according to variable parameters such as junction temperature (Tj), driving current, etc.
There can be a dramatic difference in the voltage requirement due to low temperature and the voltage requirement due to production tolerance or current difference. In the former case, the voltage requirement is only temporary, and thus the voltage head room does not need to be reserved permanently.
In the market, there are some advance LED drivers equipped with voltage adaptive function to deal with the short-term voltage requirement.
Mean Well’s HLG-480H-C, for example, has “environment adaptive” function that can automatically reduce its output current to exchange for a higher output voltage while still keep the total output power within specification rating. As the lamp is turned on and gradually warmed, the voltage falls back to a normal level and then current will also go back to the original designed value. The environment adaptive function provides 20% extra voltage head room than the common LED driver. HLG-480H-C1400 that works at 171~343V can boost to 412V temporary to ensure lamps successful startup at extremely low temperature (e.g. -40°C).
HVGC constant power series, similarly, allows a higher output voltage when current is dimmed down. There are also different possibilities for other models. If there is any question about LED startup issue, please contact MEAN WELL for the best suggestions.
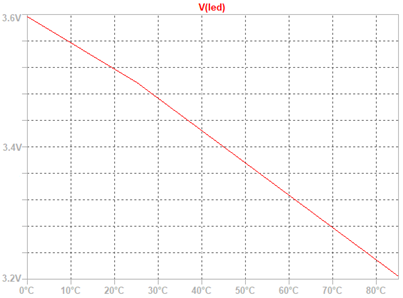
Fig. 4 Temperature vs. forward voltage
Example and Summary:
A lamp design uses 100 LEDs as in Fig. 2, driving current is 1.05A. There are 2 strings in total which mean each string has 50 LEDs. The lowest operating temperature according to the lamp spec is 0°C. To define the voltage requirement:
Solution 1 : Fill-in these parameters into PC software and get the LED operating point with margin.
Check with the manufacturer with more detail.
Solution 2 : Check LED datasheet and follow the steps below:
The LED forward voltage has a negative temperature coefficient, this means the higher the temperature the lower the forward voltage. As a LED is a self-heating element, with a proper thermal design of the lamp, the continuous working temperature and LED operating voltage are normally quite stable. The worst case comes when the lamp starts up at a low temperature. To estimate the extra voltage requirement at low temperature, LED spec provides a typical V-T curve according to the standard test condition (e.g. 350mA). Many manufacturers also provide a software tool to check voltage according to variable parameters such as junction temperature (Tj), driving current, etc.
There can be a dramatic difference in the voltage requirement due to low temperature and the voltage requirement due to production tolerance or current difference. In the former case, the voltage requirement is only temporary, and thus the voltage head room does not need to be reserved permanently.
In the market, there are some advance LED drivers equipped with voltage adaptive function to deal with the short-term voltage requirement.
Mean Well’s HLG-480H-C, for example, has “environment adaptive” function that can automatically reduce its output current to exchange for a higher output voltage while still keep the total output power within specification rating. As the lamp is turned on and gradually warmed, the voltage falls back to a normal level and then current will also go back to the original designed value. The environment adaptive function provides 20% extra voltage head room than the common LED driver. HLG-480H-C1400 that works at 171~343V can boost to 412V temporary to ensure lamps successful startup at extremely low temperature (e.g. -40°C).
HVGC constant power series, similarly, allows a higher output voltage when current is dimmed down. There are also different possibilities for other models. If there is any question about LED startup issue, please contact MEAN WELL for the best suggestions.
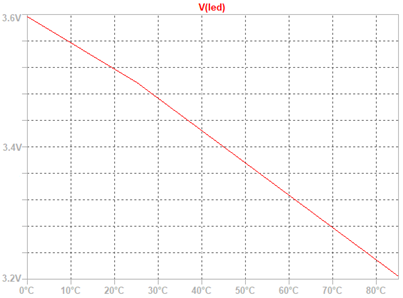
Fig. 4 Temperature vs. forward voltage
Example and Summary:
A lamp design uses 100 LEDs as in Fig. 2, driving current is 1.05A. There are 2 strings in total which mean each string has 50 LEDs. The lowest operating temperature according to the lamp spec is 0°C. To define the voltage requirement:
Solution 1 : Fill-in these parameters into PC software and get the LED operating point with margin.
Check with the manufacturer with more detail.
Solution 2 : Check LED datasheet and follow the steps below:
- Step 1: Check LED V-I curve, find the voltage on the curve according to the destinated current.
According to Fig. 2 LED typical forward voltage at 1.05A is 3.8V
- Step 2: Multiply this voltage to the number of LED in one string.
3.8 (V) x 50 (pcs) = 190 V
- Step 3: Considering production tolerance by using the ratio of max-to-type voltage.
3.48 (V) / 3.2 (V) = 108.75%
190 (V) x 108.75 % = 206.6 (V)
Short summary:
LED total forward voltage typical is 190V
LED total forward voltage worst case is 207V*
(* current ripple from the driver is not considered here.)
190 (V) x 108.75 % = 206.6 (V)
Short summary:
LED total forward voltage typical is 190V
LED total forward voltage worst case is 207V*
(* current ripple from the driver is not considered here.)
- Step 4: Considering the temperature coefficient to evaluate the worst case startup voltage.
From Fig. 4, Typ. the voltage at 0°C is 3.6V, at 85°C is 3.2V.
Assume LED lamp typically working at Tj 85°C
3.6 (V, Tj=0) / 3.2 (V, Tj=85) = 1.125 < 1.2
At cold start
LED total forward voltage typical is 190V x 1.2 = 228 V
LED total forward voltage worst case is 207V x 1.2 = 248.4 V
Suggested model: HLG-480H-C2100, reason as below
The LED lamp needs typical 190V and 2.1A (399W), in worst case 207V (435W). This is within HLG-480C rating. Further, HLG-480H has very low current ripple, thus the ripple influence to the LED voltage change can be ignored. At cold temperature, voltage requirement might temporary be over 249V, which is not within the normal constant current region, however, this situation will rarely happen and it can be covered by the environment adaptive function of HLG-480H-C2100 that maximumly support 275V with the reduced current.
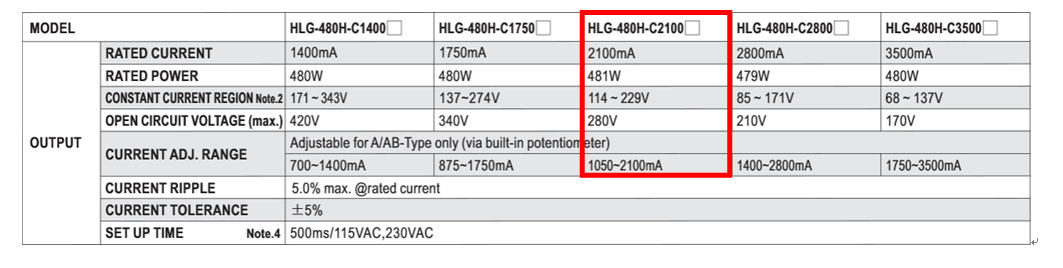
Assume LED lamp typically working at Tj 85°C
3.6 (V, Tj=0) / 3.2 (V, Tj=85) = 1.125 < 1.2
At cold start
LED total forward voltage typical is 190V x 1.2 = 228 V
LED total forward voltage worst case is 207V x 1.2 = 248.4 V
Suggested model: HLG-480H-C2100, reason as below
The LED lamp needs typical 190V and 2.1A (399W), in worst case 207V (435W). This is within HLG-480C rating. Further, HLG-480H has very low current ripple, thus the ripple influence to the LED voltage change can be ignored. At cold temperature, voltage requirement might temporary be over 249V, which is not within the normal constant current region, however, this situation will rarely happen and it can be covered by the environment adaptive function of HLG-480H-C2100 that maximumly support 275V with the reduced current.
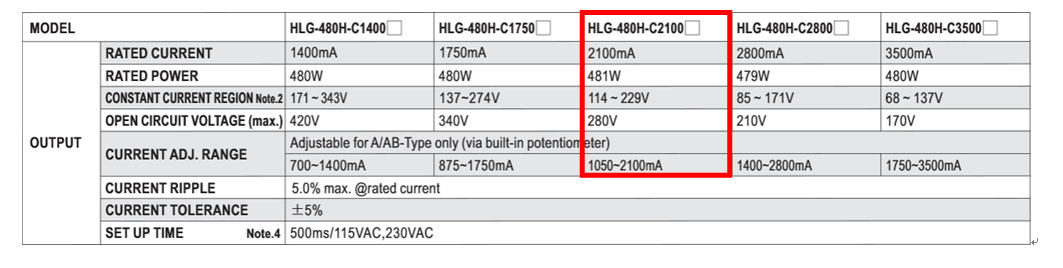
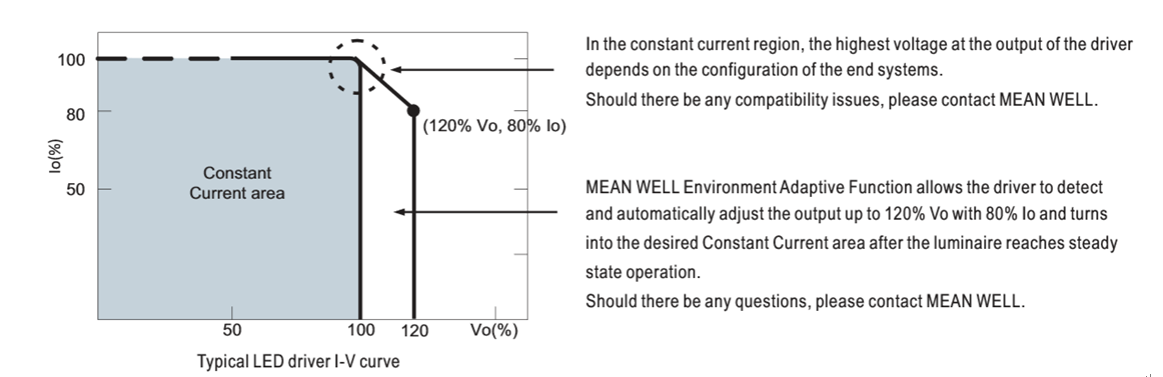